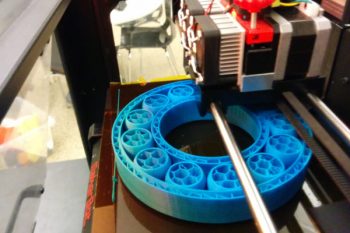
The automotive industry has a habit of pushing boundaries; with billions of dollars pumped into research and development in the industry, it’s little surprise that today’s cars look vastly different to those from even a decade ago. While much of the basic features remain the same, automotive companies are constantly looking at ways to reduce weight, lower wind resistance and make cars that look as futuristic as possible. One of the main ways they do this is to utilise modern manufacturing techniques, like 3D printing.
3D printing can, and most likely will, revolutionise manufacturing processes around the world, but transitioning this change to a larger volume industry like automobiles isn’t always as easy. Most of the 3D printing we’ve heard talk of in the automotive industry is restricted to research and development departments, and while these stories often show an amazing futuristic product, the chance of seeing these items on the roads in the next 5 years are very slim. There’s the 3D printed tire, 3D printed small cars, as well as using 3D printed materials to lower weight of components making more efficient vehicles.
Elements of 3D printing are already in use in the automotive world, from classic cars being repaired with previously unobtainable parts straight off the 3D printer, to companies offering personalised 3D printed fascias and features to customise your new vehicle. But is the 3D printer going to do away with machining in the automotive industry?
Advantages to using CNC Machining
There are still plenty of advantages to CNC machining; milling something from solid gives the finished piece a structural stability, and the layered method of most 3D printers can be inappropriate for parts that are put under strain. Similarly, it is much easier to mill a prototype headlight from acrylic than it is to 3D print one, due to the build lines running through a clear 3D print. If surface finish and precision are important on the part, these aspects are much more controllable on a CNC machine than on a 3D printer, and most 3D printed parts need a high degree of hand-finishing afterwards to get an appropriate surface finish.
CNC machining tends to involve much more waste than 3D printing, as well as often taking longer to get parts made. 3D printers can also be situated in offices, as they aren’t as noisy or messy as CNC machines. But, while 3D printing can have the advantage for small prototype parts, as parts get bigger and need to stand up to more strain, traditional CNC machining is the way to go. At Thompson Precision, we work closely with the automotive industry and we often use our fast turnaround service to offer them the best of both worlds; solid, precise parts made quickly and to the highest standards. If you have some parts that you’d like prototyping in plastic or metal, give us a call on 01277 365500 or email [email protected] and we can offer advice on the different manufacturing processes. We also have a fast prototyping service if time is of the essence.