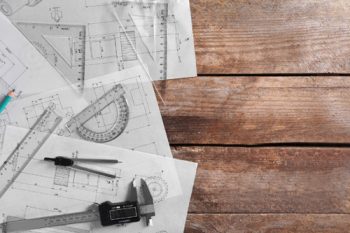
Going from concept to production in engineering can be a laborious and time-consuming process. Whether your design engineer ideas are rooted in manufacturing, structural, electrical or mechanical engineering, any concept needs to be thoroughly tested, modified and revised until it’s perfected.
With advanced technology, however, design engineers can benefit from more efficient processes and prototyping methods. Virtual prototyping can be a cost-effective and speedy way to produce an alpha prototype, for example, as it relies on specialist software to identify potential design flaws without the need for a physical prototype. Of course, many design engineers use combinations of virtual and standard prototyping, depending on the project they’re working on.
Once an alpha prototype has been created, tested and revised, design engineers begin collaborating with other engineering specialists to deliver a beta prototype. Here, components are created and assembled to check design compliance and determine whether the appropriate manufacturing or fabrication methods are being used. For case studies of projects we have worked on click here
Using precision engineering for prototyping
In order to test prototypes effectively, design engineers must have access to reliable and high-tech manufacturing and fabrication equipment. It’s critical that components are built to their exact specification so that engineers can determine whether the prototype is functioning as they intended or whether it needs further revisions.
In an industry where a tenth of a millimetre can make or break your design, it’s essential that precision engineering is used throughout the design and production process. The enhanced accuracy delivered via precision engineering is precisely what’s required when new products, machinery, and equipment is being designed and constructed, so it’s a critical and necessary element of the design and engineering process.
Managing mass production with precision engineering
Once a product has been designed, tested and refined, it can move along the production line to mass marketing. In reality, of course, the testing and refining process can be repeated numerous times until the product is fully functional and design compliant. In some cases, engineers will spend many months or years refining a design or prototype until it meets their exact requirements.
When this has been achieved, the product can be put into use. Subject to safety testing, patent applications, and launch procedures, most engineers aim for their carefully honed products to go into mass production. If a product is being mass produced, it highlights its popularity in the market, which converts into sales for the company which owns the design.
However, mass producing products which are highly technical, refined or exceptionally small in size requires specialist expertise and machinery, and this is where precision engineering comes into play. As well as enabling design engineers to create components with a high level of accuracy, precision engineering ensures that these components can be recreated again and again, without any deviation in design compliance.
Using a variety of techniques, engineers combine bespoke precision engineering equipment with computer software to enable them to produce end products which have high tolerance levels, repeatable functions, and enhanced stability. As a result, precision engineering enables design engineers to work with increased accuracy, efficiency, and productivity, as well as delivering outputs which have an increased lifespan, are exceptionally robust and can be recreated at any time.