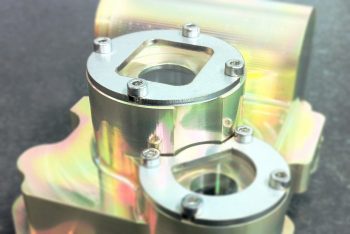
We have a long-running history of tailoring and expanding the design and manufacture process of products to assist companies achieve their goals; through our engineering experience we can help streamline projects, solve problems, recommend high quality common and exotic materials and minimise the risk of setbacks during production and assembly.
We commonly use engineering knowledge to assist our clients whenever their product needs assembling, updating or improving; one such example of this is our long relationship with a global leader in the safety instrumentation industry. This company had designed a digital camera to be used in dangerous environments, such as mining operations and oil rigs; often to be found in flammable and rugged environments, this camera had to be as safe as possible and work perfectly in tough situations.
With a working design from the client’s drawing, we were able to advise different methods of manufacturing and work with the client to streamline their project to best suit their needs. This allowed us to create a working CAD model of the different components, which then underwent multiple changes as products and manufacturing techniques evolved. We have been manufacturing different iterations of the camera case since 2009, manufactured specifically to work in hazardous environments without endangering those in the vicinity, as well as securing the data held within. In short, the camera has to be tough enough to work safely in any environment, and that kind of product development didn’t come about overnight.
We achieved this by manufacturing the main case from solid aluminium, allowing it to withstand knocks and bumps from being dropped. The case is made by putting the aluminium block through several operations on a CNC milling machine, as well as being turned using a CNC lathe. Our highly precise manufacturing methods and inspection technology allow us to ensure these parts have a tolerance of less than 20 microns, which, when paired with toughened glass and steel coverings, creates the flame path; this would dissipate a spark caused by either the battery, the flash mechanism or the internal electronics, before it could ignite the possibly flammable environment that the camera could be located.
After being machined from a solid block, the case gets anodised, which increases the resistance to corrosion and other forms of wear and tear. The case has to be manufactured to precise dimensions, or the well-defined nature of the flame path would be compromised. It also has to be as lightweight as possible; balancing the need to carry the item comfortably, as well as the function of protecting the interior workings in the case of an accident was very important to the project. Experimenting with different milling strategies at the design and prototype stages allowed us to create a balance between the case’s weight and durability.
Design and Creation
Designing and creating a product that would be safe in so many different environments, from oil rigs to coal mines, meant getting the approval of various safety organisations, including the ATEX and IECEx certifications; these certify the camera can be safely used in an explosive atmosphere. We worked with the client to ensure the drawings worked with the specifications of the regulating bodies, and we could help with any designing or manufacturing changes that needed to be made.
When developing projects like this we have to ensure trace-ability for all materials; this is the process of being able to associate the material with a sample that had undergone strict testing. This ensures that the base materials didn’t have any faults, to ensure that the products are of the highest quality and can stand up to the rigorous stresses involved.
We machine the glass for the display screen in house using a CNC machine with diamond-tipped cutters, to ensure the tolerances required by the client are met. The glass then gets heat treated to toughen it, allowing it to withstand impacts while in use. Every piece of the display glass, as well as the glass for the flash and lens covers, gets inspected by our Inspection Department using a micrometer to ensure uniformity and to exclude any pieces with imperfections. This commitment to providing high quality components ensures that every piece is up to our high standards.
We manufacture and assemble the cameras in house, with custom built tools to ensure the flame paths are the correct width, and a system to ensure all aspects of the case are given multiple inspections; we also leave pieces with glass inserts for 24 hours, to ensure that any fluctuation in temperature will not cause the tight-fitting glass to shatter.
Checks of the battery compartment and cover, the camera electronics space and push-rods for buttons are all performed, before final assembly begins. The three glass inserts are placed securely in the case, and steel coverings are screwed in to cover any gaps between glass and metal. With the camera case completed, it gets securely packaged and sent to the client.
With more than 7 years of manufacturing the different iterations of cameras and cases, we have checked and assembled thousands of components and ensured they are of the highest quality; once they leave our factory they are ready to be used in dangerous industries and challenging situations around the world.