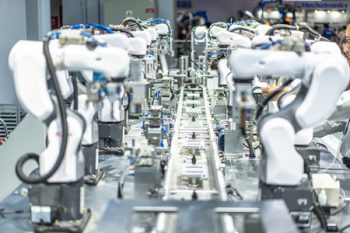
Making the journey from initial idea to mass production can be time-consuming and laborious. Whether you are new to manufacturing or have a background in the industry, it’s important to ensure any concept idea is thoroughly tested, revised and modified until it is fit for purpose.
Technology can help in the process by offering accurate and efficient methods to produce prototypes. These prototypes can easily be adjusted and honed into the perfect end result. Much cheaper and faster for any business. Prototypes can be virtual or real life, made with differing materials, a range of sizes and as complex or simple as required.
One happy that the prototype is correct, the move to testing can be made where there are a number of steps to take. Components need to be made and assemble to ensure design compliance and to make sure the correct materials and fabrication or manufacturing methods can be used.
Testing Prototypes using Precision Engineering
To be able to effectively test prototypes, the engineers involved will need to have reliable equipment as well as the required technology available to them. It is vital that all components are made to exacting specifications, without this the engineers will be unable to test whether the prototype is functioning a s it should. It is at this stage that any additional adjustments can be made if required.
Precision engineering is vital here, a tiny fraction of a millimetre can mean the difference between your design working at its optimum or not. That’s why we employ precision engineering techniques throughout the entire process. This enhanced accuracy is necessary in the inception of new products, components and machinery and therefore is an essential element in the design and engineering process of mass production.
Moving to Mass Production
At the point at which the product has been fully tested it’s time to move to mass production. In reality the product may spend its lifetime being improved and adjusted, depending what it is of course. But once it is fit for purpose, meaning fully functional and compliant with the design it is ready to go onto the production line and be made in bigger quantities.
It’s important to note that the mass production of complex or technical products requires specialist expertise and machinery to ensure it maintains the correct level of quality. This is why working with Precision Engineers is the only way to ensure your product maintains its exacting requirement when produced is large quantities. It’s easy to see the degradation of products over time and this is why regular checking and testing needs to take place.
Precision engineering expertise and techniques allow engineers to product accurate, efficient and cost-effective outputs, increasing their lifespan. Once completed, the product can be recreated and brought back onto the production line time and time again. When done properly the product made 5 years after the first run, should be just as good if not better than the first.
To find out more about our precision engineering projects, please take a look at our case studies.