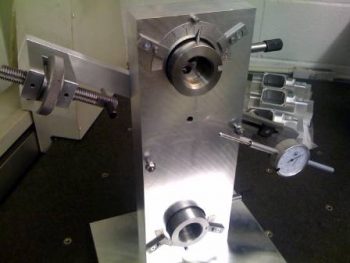
Computer Numerical Control (CNC) machining has revolutionised the manufacturing process in various industries, and aerospace is no exception. CNC machining allows for the precise and efficient production of complex parts, making it an essential technology in aerospace manufacturing. The aerospace industry requires high precision, accuracy, and reliability in its products, and CNC machining helps meet these demands. This article will delve into the various applications of CNC machining in aerospace manufacturing, highlighting its significance and recent advancements in the field.
Advantages of CNC Machining in Aerospace Manufacturing
CNC machining offers several advantages in aerospace manufacturing, making it a widely used process in the industry. One of the key benefits of CNC machining is precision and accuracy in parts production. The use of computer-controlled machines allows for exact dimensions and tolerances to be achieved, ensuring that each part meets strict industry standards. This level of accuracy is fundamental in aerospace where safety and performance are critical factors.
Another advantage of CNC machining is high speed and efficiency in production processes without sacrificing quality. With the ability to operate at high speeds and perform multiple operations simultaneously, CNC machines significantly reduce production time and labour costs. Additionally, CNC machining can produce complex shapes and designs that would be difficult or impossible to achieve with traditional manufacturing methods. This allows aerospace engineers to design more sophisticated and efficient parts, such as those found in aircraft engines, fuel systems, and structural components.
Aerospace Materials Used in CNC Machining
In the aerospace industry, the materials used in CNC machining play a crucial role in ensuring the safety and performance of aircraft and spacecraft. Aluminium alloys are commonly used in aerospace manufacturing due to their lightweight, durability, and corrosion resistance. They are often used in structures, skin, and rivets. Titanium alloys are also popular in aerospace manufacturing due to their high strength-to-weight ratio, corrosion resistance, and ability to withstand extreme temperatures. They are often used in engine components, fasteners, and structural components.
Steel alloys are another popular choice in aerospace manufacturing due to their high strength, toughness, and resistance to fatigue. They are often used in landing gear, engine mounts, and other structural components. Composite materials, made from a combination of materials such as carbon fibre-reinforced polymers (CFRP), glass fibre-reinforced polymers (GFRP), and aramid fibres, are also increasingly being used in aerospace manufacturing. These materials offer many benefits including light weight, high strength, and fatigue resistance. They are often used in wings, fuselage, and empennage.
In addition to these materials, there are other specialised materials used in aerospace manufacturing that require specific machining techniques. For example, ceramic matrix composites (CMCs) are used in high-temperature applications such as heat shields and thermal protection systems. These materials are extremely hard and require specialised cutting tools and techniques to machine. Another example is advanced superalloys, which are used in high-temperature applications such as gas turbines and jet engine components. These materials have excellent high-temperature strength but are very difficult to machine due to their hardness and toughness.
Applications of CNC Machining in the Aerospace Industry
CNC machining is extensively used in the production of structural components, such as wing spars and ribs, fuselage frames and bulkheads, and landing gear components. These parts form the backbone of an aircraft and must be manufactured to exacting standards to ensure the safety and reliability of the aircraft.
Flight control surfaces, such as ailerons, elevators, and rudders, as well as flaps and slats, are also produced using CNC machining techniques. These components are critical to the stability and manoeuvrability of an aircraft and must be precisely manufactured to ensure proper flight dynamics.
Another application of CNC machining in the aerospace industry is in the production of high-precision jigs and fixtures for the assembly and inspection of aircraft parts. These jigs and fixtures must be manufactured to exacting standards to ensure proper alignment and fit of parts, and CNC machining enables the production of complex geometries and precise dimensions with ease.
CNC machining is also used in the production of aerospace test gauges, which are used to measure the performance and functionality of aerospace components. These gauges must be manufactured to strict standards to ensure accurate and reliable measurements, and CNC machining enables the production of complex shapes and profiles with precision and accuracy.
The aerospace industry also relies heavily on CNC machining for the production of spacecraft components, such as satellite parts, including bus structures and solar panel mounts, as well as rocket components, like fairings and heat shields. These components must be able to withstand the harsh conditions of space and function accurately under extreme temperatures and pressures.
Challenges and Limitations of CNC Machining in Aerospace Industry
The aerospace industry imposes stringent quality and safety requirements on all components, which presents significant challenges for CNC machining. The industry demands exceptional accuracy, surface finish, and dimensional tolerances, which requires a high degree of skill and attention to detail. Moreover, some aerospace materials are notoriously difficult to machine, such as titanium and Inconel, which pose significant challenges for even the most experienced machinists.
Additionally, some part geometries are so complex that they require specialised equipment and expertise to machine effectively. For instance, parts with intricate contours, deep pockets, and narrow channels can be difficult to access with standard cutting tools, requiring customised solutions.
In summary, CNC machining has revolutionised the aerospace manufacturing industry by offering numerous benefits, including improved accuracy, faster production times, reduced material waste, and increased productivity. With the ability to produce complex shapes and profiles with ease, CNC machining has enabled the creation of lighter, stronger, and more durable aircraft components. Furthermore, the use of CNC machining has allowed for the production of parts with tighter tolerances, resulting in improved safety and performance. As the demand for air travel continues to grow, the importance of CNC machining in aerospace manufacturing will only continue to increase.