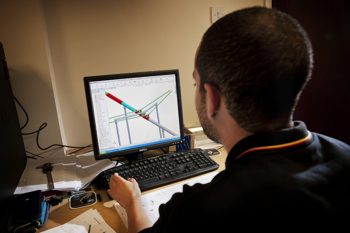
Reverse engineering is where something (in this case a product or component) is taken apart to understand how it was put constructed in the first place. It is used in all walks of life in situations where you examine the end result and try and work out how to get there.
It could be applied to pretty much anything, in this post however, we are going to look at reverse engineering when applied to a product, assembly, part or component. In this case it is often used for obsolete parts which are no longer in production or to understand a competitor’s product better or to work out how to create something similar.
The process itself depends on what is found once the project has started, it may be fairly easy and simple or it could take multiple iterations in more complex scenarios.
Reverse Engineering Knowledge
It is years of experience collating a wealth of knowledge that has allowed Thompson Precision to product high quality results quickly. We team our expertise with the latest technologies such as laser scanning, 3D printing and Solidworks design software.
We are often asked to reverse engineer products, components or assemblies that have ceased production or are obsolete. Understanding how these things were made in the first place means that we can apply the right methods and use the right materials.
There’s no point using high tech materials to produce a part that is going to be used in a machine that’s 30 years old if it means that part won’t gel perfectly, this could cause undue stress and wear on the existing parts. This is where having traditional skills to compliment new technologies comes into its own.
Use of Technology in Reverse Engineering
If an existing part is in existence then we can often scan that part using a laser. This scan is fed into our system and specialist software is used to create a 3D drawing of whatever whas scanned. If a part isn’t available but the drawings of the original one are in existence, then these can also be used and fed into our system. From this scan or from drawings, we can create a 3D model, this is used to cast the end product, component or assembly.
We have the ability to quickly use reverse engineering to create variations using slightly different mechanics, designs or materials to work out what works best both independently or how it works as part of a larger mechanism or product.
This use of more modern techniques allows a much quicker and smoother process overall with less costly reiterations required alongside a much better end result.