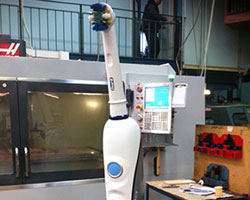
Reverse engineering is when a product manufactured by someone else is reproduced after examining its construction and composition – it is a process which involves disassembling or deconstructing the product, analysing its components and workings and then producing something similar or the same. It is also known as ‘back engineering’.
While this might at first sound like a process for ripping something off (and it can be, particularly for military purposes), it is in fact also a legally sanctioned method of copying a technology and it has some very useful applications. Patent infringement where applicable, is avoided by using different techniques or mechanisms to produce the same results
An application where reverse engineering is particularly useful is when a part or component required is no longer being manufactured. As an example Thompson Precision were able to reproduce a vital train steering component for London Underground. They had depleted their stock and were unable to purchase the part from the original manufacturer. There were also no drawings or specifications available, so we used reverse engineering to determine how to manufacture the component for them, and in fact upgraded it so that it was even better than the original. Read our case study for more information.
Other ways Reverse Engineering is useful
Obsolescence is a prime reason for reverse engineering. When parts are no longer made but technology or machinery is still utilising these components, being able to reverse engineer the parts is the only way to keep things running without replacing the whole system. Conversely, when parts themselves become obsolete, they can be reused or repurposed in a different way by employing reverse engineering.
Reverse engineering is also useful for learning. In addition to learning how existing components or systems work, it’s also possible to go back and understand the key issues of an ineffective design in order to improve it and make it work.
It can be applied to components, assemblies or even whole products. Apart from allowing reproduction, it also teaches us a lot about how many items were originally made – technology and history that might otherwise have disappeared.
When obsolete or historical components are analysed, as well as being reproduced, they can often also be improved on, combining the knowledge from reverse engineering older parts with the advanced technology of today. As in our London Underground example, this gives the best of both worlds.
However using the latest technology to create ‘perfect’ new parts from less perfect originals, isn’t always the right thing to do, and this is where the right knowledge and experience is essential. For instance if it’s important that the reproduction has exactly the same appearance as the original in order to look authentic, traditional methods of manufacture can still be employed to build the component after the composition has been analysed. Another situation where improving the reproductions too much can be detrimental, is when the component will be operating together with other original parts. If the new part is too ‘perfect’ and efficient it may put the older parts under extra stress and this could lead to excessive wear or even failure.
It is therefore crucial that reverse engineering is undertaken by a company with both the knowledge and experience of the technology used historically and an understanding of the most up to date production methods. Find out more about Thompson Precision’s reverse engineering credentials here.